生物質(zhì)燃燒產(chǎn)生的SO2主要來源于燃料中有機(jī)硫的氧化和硫酸鹽的熱分解,與生物質(zhì)燃料品種有關(guān)。目前,為降低SO2的排放指標(biāo),生物質(zhì)發(fā)電廠可采用的脫硫技術(shù)包括:爐內(nèi)脫硫、半干法脫硫(SDA、CFB)、干法脫硫(SDS)以及濕法脫硫等。
The SO2 generated by biomass combustion mainly comes from the oxidation of organic sulfur in the fuel and the thermal decomposition of sulfate, which is related to the variety of biomass fuel. At present, in order to reduce the emission indicators of SO2, the desulfurization technologies that biomass power plants can adopt include: furnace desulfurization, semi dry desulfurization (SDA, CFB), dry desulfurization (SDS), and wet desulfurization.
3.1爐內(nèi)石灰石脫硫
3.1 Limestone desulfurization in the furnace
爐內(nèi)石灰石脫硫技術(shù)是通過向爐內(nèi)直接添加石灰石粉來控制SO2的排放。投入爐內(nèi)的石灰石在850℃左右條件下發(fā)生鍛燒反應(yīng)生成氧化鈣,然后氧化鈣、SO2和氧氣經(jīng)過一些列化學(xué)反應(yīng),終生成硫酸鈣,化學(xué)反應(yīng)式為:
The limestone desulfurization technology in the furnace controls SO2 emissions by directly adding limestone powder to the furnace. The limestone put into the furnace undergoes calcination reaction at about 850 ℃ to generate Calcium oxide, and then Calcium oxide, SO2 and oxygen undergo a series of chemical reactions to finally generate calcium sulfate. The chemical reaction formula is:
CaCO3→CaO+CO2 (煅燒反應(yīng))
CaCO3 → CaO+CO2 (calcination reaction)
CaO+SO2+1/2O2→CaSO4 (固硫反應(yīng))
CaO+SO2+1/2O2 → CaSO4 (sulfur fixation reaction)
國內(nèi)燃煤流化床鍋爐爐內(nèi)脫硫效率一般達(dá)60%,生物質(zhì)循環(huán)流化床鍋爐爐內(nèi)噴鈣脫硫的效率比傳統(tǒng)燃煤循環(huán)流化床鍋爐低,大約在50%左右。甚至更低,要獲得更高的脫硫效率,需考慮爐后脫硫。
The desulfurization efficiency of coal-fired fluidized bed boilers in China is generally up to 60%, while the efficiency of calcium injection desulfurization in biomass circulating fluidized bed boilers is lower than that of traditional coal-fired circulating fluidized bed boilers, which is about 50%. Even lower, in order to achieve higher desulfurization efficiency, it is necessary to consider desulfurization after the furnace.
3.2 SDA旋轉(zhuǎn)噴霧半干法脫硫
3.2 SDA rotary spray semi dry desulfurization
半干法脫硫常用的工藝為SDA旋轉(zhuǎn)噴霧半干法。SDA法的工藝流程為:石灰制備系統(tǒng)將熟石灰制備成一定濃度的Ca(OH)2漿液,該漿液經(jīng)過旋轉(zhuǎn)霧化器噴入半干式反應(yīng)塔中,形成極小的霧滴,噴入100~150℃鍋爐出口煙氣中,煙氣與石灰漿液霧滴充分接觸發(fā)生物理、化學(xué)反應(yīng),氣體中的SO2等酸性其他被吸收凈化。同時(shí),部分與氧氣發(fā)生氧化反應(yīng),使CaSO3轉(zhuǎn)化為CaSO4。反應(yīng)式為:
The most commonly used process for semi dry desulfurization is SDA rotary spray semi dry process. The process flow of the SDA method is as follows: the lime preparation system prepares hydrated lime into a certain concentration of Ca (OH) 2 slurry. The slurry is sprayed into a semi dry reaction tower through a rotary atomizer to form extremely small droplets, which are sprayed into the flue gas at the outlet of the 100-150 ℃ boiler. The flue gas and lime slurry droplets come into full contact and undergo physical and chemical reactions, and acidic substances such as SO2 in the gas are absorbed and purified. At the same time, some undergo oxidation reaction with oxygen, converting CaSO3 into CaSO4. The reaction formula is:
SO2+ Ca(OH)2→CaSO3+ H2O
SO2+Ca (OH) 2 → CaSO3+H2O
SO2+ 1/2O2+ Ca(OH)2→CaSO4+ H2O
SO2+1/2O2+Ca (OH) 2 → CaSO4+H2O
SO3+Ca(OH)2→CaSO4+ H2O
SO3+Ca (OH) 2 → CaSO4+H2O
2HCl+Ca(OH)2→CaCl2+ H2O
2HCl+Ca (OH) 2 → CaCl2+H2O
2HF+Ca(OH)2→CaF2+ H2O
2HF+Ca (OH) 2 → CaF2+H2O
SDA脫硫工藝特點(diǎn):脫硫效率高達(dá)98%以上;SDA工藝系統(tǒng)結(jié)構(gòu)簡單,調(diào)節(jié)靈活,可控性好;濕法脫硫的機(jī)理,干法的特點(diǎn);無廢水產(chǎn)生,系統(tǒng)不需防腐處理。
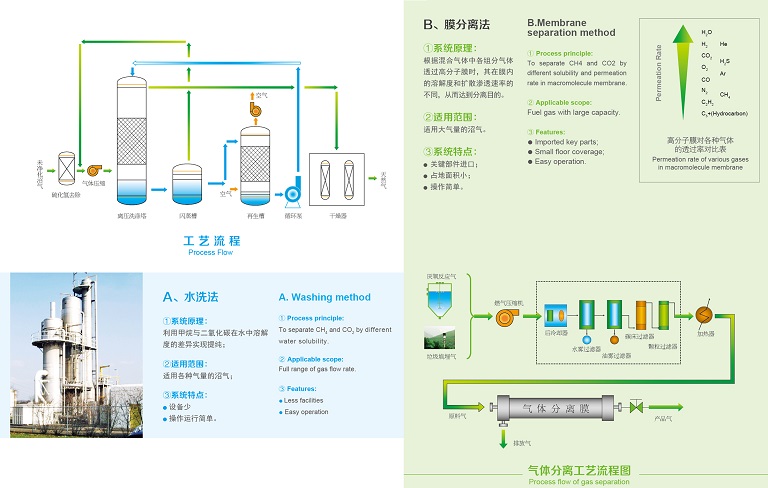
SDA desulfurization process features: desulfurization efficiency can reach over 98%; The SDA process system has a simple structure, flexible adjustment, and good controllability; The mechanism of wet desulfurization and the characteristics of dry method; No wastewater is generated, and the system does not require anti-corrosion treatment.
3.3 CFB循環(huán)流化床半干法脫硫
3.3 CFB circulating fluidized bed semi dry desulfurization
循環(huán)流化床煙氣脫硫工藝的原理是:脫硫劑Ca(OH)2粉末和煙氣中的SO2,在有水參與的情況下,在Ca(OH)2粒子的液相表面發(fā)生反應(yīng),反應(yīng)機(jī)理與SDA旋轉(zhuǎn)噴霧干燥相同。其主要反應(yīng)發(fā)生在100~150℃脫硫反應(yīng)塔內(nèi),Ca(OH)2粉末、煙氣及噴入的水分,在流化狀態(tài)下充分混合,此時(shí)由于有水參與,Ca(OH)2粉末表面離子化,煙氣中的酸性氣體與Ca2+接觸并迅速反應(yīng)。
The principle of circulating fluidized bed flue gas desulfurization process is that the desulfurization agent Ca (OH) 2 powder and SO2 in flue gas react on the liquid surface of Ca (OH) 2 particles with the participation of water. The reaction mechanism is the same as SDA rotary spray drying. The main reaction occurs in a desulfurization reaction tower at 100-150 ℃. Ca (OH) 2 powder, flue gas, and injected water are fully mixed in a fluidized state. At this time, due to the participation of water, the surface of Ca (OH) 2 powder ionizes, and the acidic gas in the flue gas comes into contact with Ca2+and reacts rapidly.
由于有物料再循環(huán)系統(tǒng),使得脫硫塔內(nèi)參加反應(yīng)的Ca(OH)2量遠(yuǎn)遠(yuǎn)大于新投加的Ca(OH)2量,即實(shí)際反應(yīng)的脫硫劑與酸性氣體的摩爾比遠(yuǎn)遠(yuǎn)大于表觀摩爾比,從而使SO2、SO3、HCl、HF等酸性氣體能被充分地吸收,實(shí)現(xiàn)高效脫硫。
Due to the presence of a material recycling system, the amount of Ca (OH) 2 participating in the reaction in the desulfurization tower is much greater than the newly added Ca (OH) 2. This means that the molar ratio of the actual reaction desulfurizer to the acidic gas is much greater than the apparent molar ratio, allowing acidic gases such as SO2, SO3, HCl, HF, etc. to be fully absorbed, achieving efficient desulfurization.
CFB主要工藝特點(diǎn):煙氣、物料、水在劇烈的摻混升降運(yùn)動(dòng)中接觸時(shí)間長、混合充分,脫硫效率達(dá)到90%;不產(chǎn)生廢水,不需要設(shè)置廢水處理系統(tǒng);尾部煙囪不需要防腐。
The main process characteristics of CFB include long contact time and sufficient mixing of flue gas, materials, and water during intense mixing and lifting movements, with a desulfurization efficiency of 90%; No wastewater is generated and there is no need to set up a wastewater treatment system; The tail chimney does not require anti-corrosion.
3.4 SDS干法脫硫
3.4 SDS dry desulfurization
SDS干法脫硫可采用堿性吸收劑噴射,在鍋爐出口后端合適位置增加碳酸氫鈉超細(xì)粉噴射口,使其與180~250℃煙氣中的SO2發(fā)生化學(xué)反應(yīng),如:
SDS dry desulfurization can be achieved by using alkaline absorbent injection, and adding a sodium bicarbonate ultrafine powder injection port at a suitable position at the rear end of the boiler outlet to chemically react with SO2 in the flue gas at 180-250 ℃, such as:
2NaHCO3+熱量-----Na2CO3+ CO2+ H2O
2NaHCO3+Heat - Na2CO3+CO2+H2O
Na2CO3+ SO2+ 1/2 O2+ 熱量-----Na2SO4+ CO2
Na2CO3+SO2+1/2 O2+Heat - Na2SO4+CO2
SDS工藝主要技術(shù)特點(diǎn):脫硫效率可達(dá)95%以上;對(duì)煙氣流量、SO2濃度等工況的變化適應(yīng)性較強(qiáng);脫硫劑成本較高,總體運(yùn)行成本相對(duì)較高,適用于煙氣含硫量低(或煙氣量?。?,總消耗量不大,這樣吸收劑增加的成本不敏感;腐蝕性輕微,基本不用采取特殊防腐措施,但需采取相應(yīng)防磨措施;由于脫硫工藝不需要對(duì)煙氣進(jìn)行了増濕減溫,排放煙氣溫度基本沒有降低,煙氣排放始終保持良好的視覺效果;系統(tǒng)不產(chǎn)生廢水。由于SDS反應(yīng)窗口溫區(qū)(即煙氣溫度180~250℃),這樣才能保證90%以上的脫硫效率。對(duì)于生物質(zhì)鍋爐采用SDS干法脫硫系統(tǒng),由于生物質(zhì)鍋爐一般的排煙溫度是較低,一般是130-150℃,為了保證較高的脫硫效率,需將鍋爐煙氣升溫,造成運(yùn)行成本的大大增加。
The main technical characteristics of the SDS process are: the desulfurization efficiency can reach over 95%; Strong adaptability to changes in flue gas flow rate, SO2 concentration, and other operating conditions; The cost of desulfurizers is relatively high, and the overall operating cost is relatively high. It is suitable for flue gas with low sulfur content (or small flue gas content), and the total consumption is not large, so the increased cost of absorbers is not sensitive; Slightly corrosive, no special anti-corrosion measures need to be taken, but corresponding anti wear measures need to be taken; Due to the fact that the desulfurization process does not require humidification and temperature reduction of the flue gas, the temperature of the discharged flue gas remains basically unchanged, and the flue gas emissions always maintain a good visual effect; The system does not produce wastewater. Due to the temperature range of the SDS reaction window (i.e. flue gas temperature of 180-250 ℃), it is necessary to ensure a desulfurization efficiency of over 90%. For biomass boilers using SDS dry desulfurization system, due to the generally low exhaust gas temperature of biomass boilers, which is generally 130-150 ℃, in order to ensure high desulfurization efficiency, it is necessary to raise the temperature of the boiler flue gas, resulting in a significant increase in operating costs.
3.5濕法脫硫
3.5 Wet desulfurization
濕法脫硫采用石灰石漿液、氫氧化鈉溶液或者氨水等堿性溶液與煙氣接觸,吸收液通過高效噴嘴霧化噴入吸收塔,分散成細(xì)小的液滴并覆蓋吸收塔的整個(gè)斷面。液滴中的堿液與塔內(nèi)煙氣逆流充分接觸,發(fā)生傳質(zhì)與吸收反應(yīng),煙氣中的SO2、SO3等被堿液吸收。
Wet desulfurization uses alkaline solutions such as limestone slurry, sodium hydroxide solution or ammonia water to contact with flue gas, and the absorption liquid is sprayed into the absorption tower through high-efficiency nozzle atomization to disperse into small droplets and cover the entire section of the absorption tower. The alkali solution in the droplet fully contacts the flue gas in the tower in countercurrent, leading to mass transfer and absorption reactions. SO2, SO3, and other substances in the flue gas are absorbed by the alkali solution.
該工藝的特點(diǎn)是:技術(shù)比較成熟,脫硫效率高(90~98%);適應(yīng)性強(qiáng),能適應(yīng)高濃度SO2煙氣條件;產(chǎn)生脫硫廢水;系統(tǒng)復(fù)雜,幾乎所有設(shè)備都需防腐;排煙溫度低于煙氣露點(diǎn)溫度,煙囪需要做防腐。煙囪排煙存在煙羽問題、脫硫廢水二次污染問題。
The characteristics of this process are: relatively mature technology, high desulfurization efficiency (90-98%); Strong adaptability, able to adapt to high concentration SO2 flue gas conditions; Generate desulfurization wastewater; The system is complex, and almost all Almost all needs anti-corrosion; The exhaust temperature is lower than the dew point temperature of the flue gas, and the chimney needs to be protected against corrosion. There are issues with smoke plumes and secondary pollution of desulfurization wastewater in chimney smoke exhaust.
4.生物質(zhì)鍋爐脫硫脫硝推薦工藝分析
4. Analysis of recommended processes for desulfurization and denitrification of biomass boilers
針對(duì)20萬標(biāo)方煙氣,排煙120~140℃的生物質(zhì)鍋爐,NOx、SO2的原始排放濃度均為400 mg/Nm3,排放濃度分別為50、35 mg/Nm3。
For biomass boilers with 200000 standard cubic meters of flue gas and smoke exhaust of 120-140 ℃, the original emission concentrations of NOx and SO2 are both 400 mg/Nm3, with emission concentrations of 50 and 35 mg/Nm3, respectively.
脫硝推薦采用SNCR+SCR聯(lián)合脫硝技術(shù),把SNCR工藝的還原劑噴入爐膛技術(shù)同SCR工藝?yán)锰右莅边M(jìn)行催化反應(yīng)的技術(shù)結(jié)合起來,進(jìn)一步脫除NOx;它是把SNCR工藝的低費(fèi)用的特點(diǎn)同SCR工藝的高效率進(jìn)行有效結(jié)合。SNCR將煙氣中NOx濃度降至200 mg/Nm3,再通過SCR將NOx降至50mg/Nm3;脫硫有SDA半干法、CFB半干法、鈉減法濕法三種脫硫工藝可供選擇。脫硫脫硝設(shè)備投資與運(yùn)行費(fèi)用如表4.1所示。
It is recommended to use the SNCR+SCR combined denitrification technology, which combines the technology of spraying the reducing agent of the SNCR process into the furnace with the technology of using escaped ammonia for catalytic reaction in the SCR process to further remove NOx; It effectively combines the low cost characteristics of SNCR process with the high efficiency of SCR process. SNCR reduces the NOx concentration in flue gas to 200 mg/Nm3, and then SCR reduces NOx to 50mg/Nm3; There are three desulfurization processes available for selection: SDA semi dry method, CFB semi dry method, and sodium reduction wet method. The investment and operating costs of desulfurization and denitrification equipment are shown in Table 4.1.
表4.1 設(shè)備投資與運(yùn)行費(fèi)用
Table 4.1 Equipment Investment and Operating Costs
圖片?
Picture?
SNCR和SCR還原劑采用尿素,SNCR工藝在脫除部分NOx的同時(shí)也為后面的SCR提供所需要的氨,可以省卻尿素?zé)峤鈬娚湎到y(tǒng)的設(shè)置。對(duì)于沒有設(shè)置SNCR的系統(tǒng),若需增設(shè)補(bǔ)氨系統(tǒng),采用尿素?zé)峤夤に?,設(shè)備投資費(fèi)用需要另增加75萬元,運(yùn)行費(fèi)用每年增加80萬元。
The SNCR and SCR reducing agents use urea, and the SNCR process not only removes some NOx but also provides the required ammonia for subsequent SCR, which can save the setting of the urea pyrolysis injection system. For systems without SNCR, if an ammonia replenishment system needs to be added and a urea pyrolysis process is adopted, the equipment investment cost will need to be increased by 750000 yuan, and the operating cost will increase by 800000 yuan annually.
生物質(zhì)鍋爐可行的脫硫技術(shù)有半干法(SDA、CFB)和濕法脫硫。與半干法脫硫相比,濕法脫硫產(chǎn)生脫硫廢水,存在二次污染問題;雖然鈉堿濕法脫硫總體投資比半干法脫硫省20~30%,但運(yùn)行成本每年高出半干法500萬。
The feasible desulfurization technologies for biomass boilers include semi dry (SDA, CFB) and wet desulfurization. Compared with semi dry desulfurization, wet desulfurization generates desulfurization wastewater, which poses a secondary pollution problem; Although the overall investment of sodium alkali wet desulfurization is 20-30% less than that of semi dry desulfurization, the operating cost is 5 million yuan higher per year than that of semi dry desulfurization.
CFB循環(huán)流化床半干法脫硫技術(shù)與SDA相比,運(yùn)行成本基本持平,但投資成本高300萬,且系統(tǒng)相對(duì)復(fù)雜,維護(hù)不方便。
Compared with SDA, the CFB circulating fluidized bed semi dry desulfurization technology has almost the same operating cost, but the investment cost is 3 million yuan higher, and the system is relatively complex and inconvenient to maintain.